At a Glance
- AI-powered digital twins simulate real-world conditions to improve the design and performance of EV motors and batteries.
- These digital models enable predictive maintenance, enhancing battery efficiency, and longevity—crucial for adopting electric vehicles.
- By collaborating with AI-driven models, engineers can significantly reduce development time, “accelerating the EV revolution” and bringing innovations to market faster.
Discover how AI-powered digital twins are revolutionising the future of electric vehicles (EVs) by offering real-time insights and optimising performance, especially for traction motors and batteries. This article delves into the transformative role of AI and GenAI, highlighting their impact on design, predictive maintenance, and energy efficiency. Get ready to explore how these innovations are set to drive the next era of sustainable electric mobility.
Understanding AI-enhanced Digital Twins
Meet the ultimate game-changer: AI-enhanced digital twins!
These virtual doppelgängers of your EV’s traction motors and batteries track their entire lifecycle in real-time, offering unparalleled insights and smarts. Traditional twins are cool, but with AI, we’re leaping to light speed.
Imagine this: Faster EV battery design, predictive magic that spots issues before they become problems, and adaptive learning that handles all the twisty, non-linear behaviours. These digital twins don’t just monitor—they learn and decide, making your EV more reliable and boosting customer trust.
But that’s not all. AI-enabled twins can quickly sort batteries based on their State of Health (below 70%-80%), deciding if they’re headed for a second life in stationary energy storage or the recycling bin. This supercharged optimisation of performance, energy consumption, and maintenance schedules means your EV runs smoother, lasts longer, and stays greener.
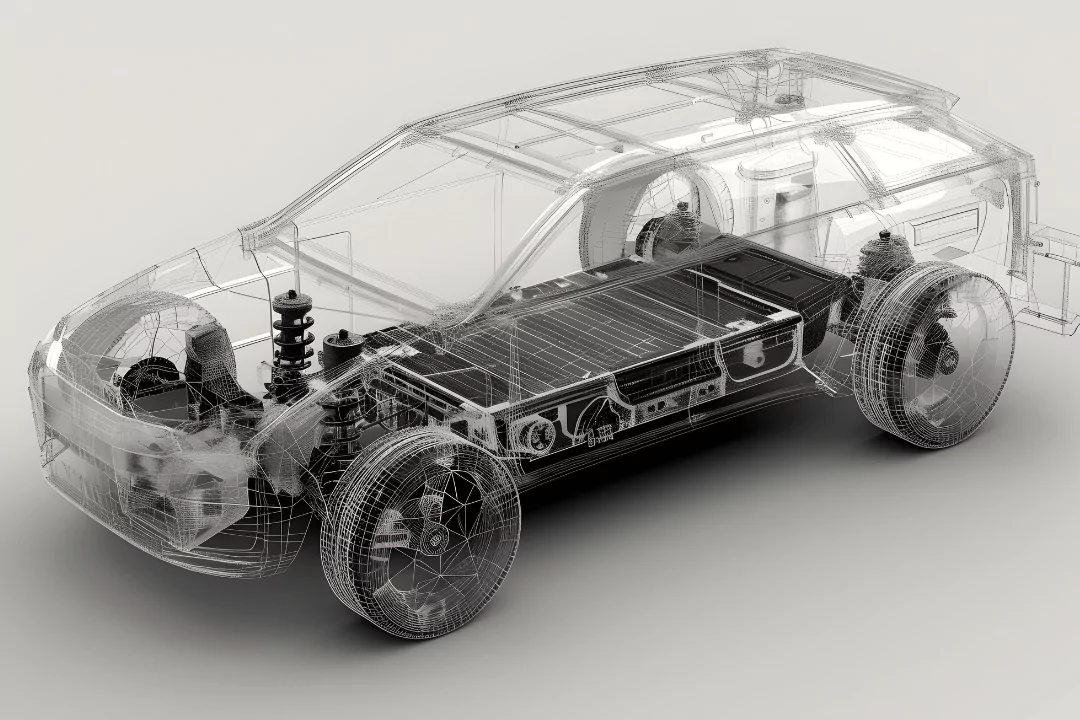
Key Enablers for Digital Twins in EV’s
- High-Performance Computing: This can be used to simulate and test electric drivetrain components under various conditions. By running complex simulations, OEMs can analyse thermal behaviour, mechanical stresses, and electromagnetic fields. This accelerates the design process, reduces the need for physical prototypes, and helps in optimising the efficiency and durability of electric motors and batteries.
- Advanced Sensors: Integrating advanced sensors into EVs can help monitor the health and performance of critical components such as batteries and motors. These sensors collect data on temperature, vibration, and electrical parameters, which are then used to create accurate digital twins. This real-time monitoring allows for predictive maintenance and optimisation of vehicle performance, enhancing reliability and customer satisfaction.
- IoT, Cloud and 5G Connectivity: It leverages IoT, cloud computing, and 5G connectivity to provide real-time data and analytics for EVs throughout. This connectivity enables continuous data flow between a vehicle and the cloud, allowing for remote diagnostics, over-the-air updates, and real-time navigation assistance. The integration of 5G ensures low latency and high bandwidth, which is essential for the seamless operation and communication of digital twins.
- AI and Machine Learning: By deploying machine learning algorithms OEMs can analyse driving patterns and optimise energy consumption. OEMs can also predict maintenance needs. By analysing data from various sensors these algorithms can help ensure that the vehicles operate at peak likelihood of the efficiency, thereby reducing unexpected breakdowns.
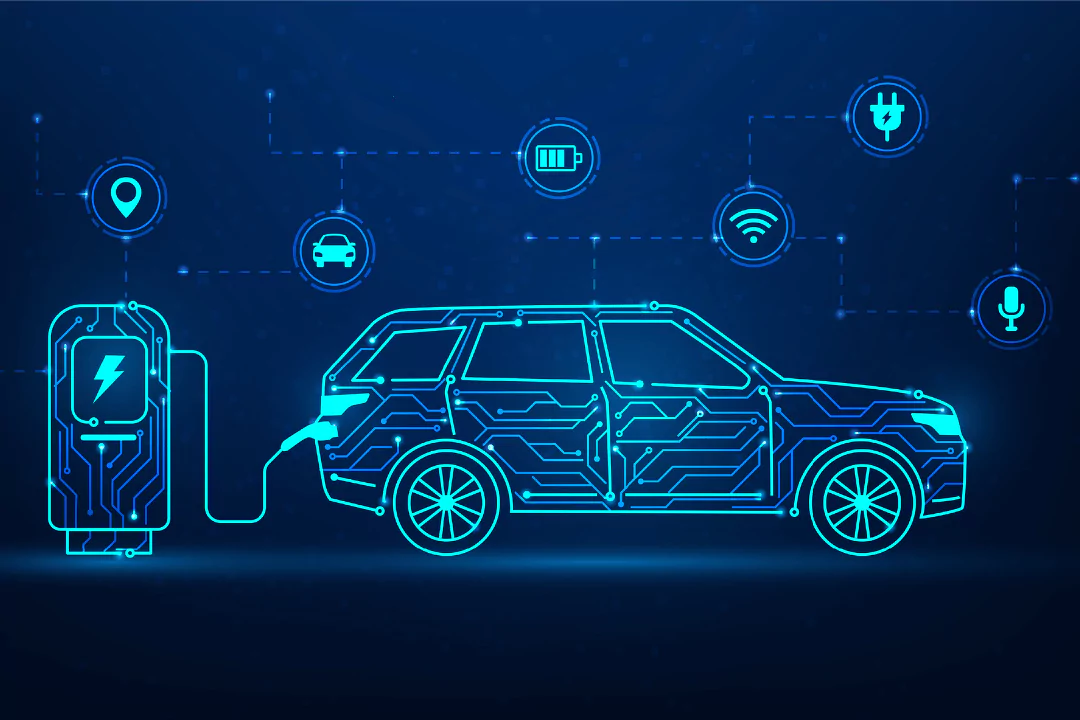
Use Cases and Applications of AI in EVs
Here’s a sneak peek of the components typically involved in such a framework:
AI-enhanced digital twins are the ultimate multitaskers for EVs, revolutionising everything from design to maintenance.
For traction motors, digital twins can simulate electromagnetic fields, thermal behaviour, and mechanical stresses, enabling designers to optimise motor efficiency and longevity.
When it comes to batteries, these twins dive into the electrochemical processes, tracking thermal dynamics and ageing characteristics to optimise cell selection and design.
Here’s how they can help in the next-gen battery development:
- Generative Design: Traction motor and battery Digital Twin designs are backed by real historical data that highly correlates with the physical system. These digital twins speed up the early design stage, cutting time and costs. They help pick the best materials and simulate all kinds of scenarios, making sure your designs are spot on. Plus, they make rolling out new designs a breeze with virtual testing and validation. Generative design also has the intelligence of maturing the designs based on the inputs that are coming from the field in future iterations. It also enables to design for manufacturability and serviceability and achieving first-time right designs.
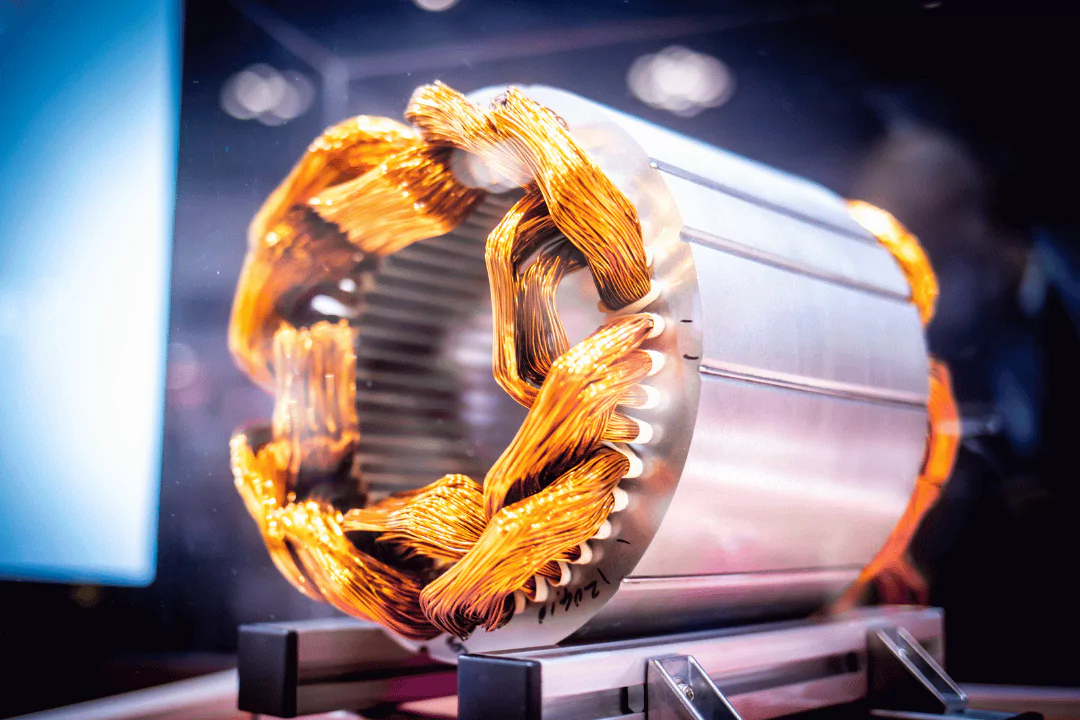
- Advanced Material Selection: AI algorithms to analyse the properties of various materials and predict their performance in battery cells. This helps in selecting materials that offer the best energy density, longevity, and thermal stability, leading to improved battery performance and safety. AI-driven simulations can also help identify optimal combinations of materials for lithium-ion batteries, which are critical for the performance and safety of their EVs.
- Battery Condition Monitoring and Performance Optimisation: AI and ML algorithms can continuously keep an eye on your battery’s health, tweaking settings to optimise the performance of both the traction motor and battery under all sorts of conditions. They can alert drivers and OEMs about maintenance needs and part replacements and even suggest the best charging schedules and usage patterns to squeeze every last mile out of your battery.
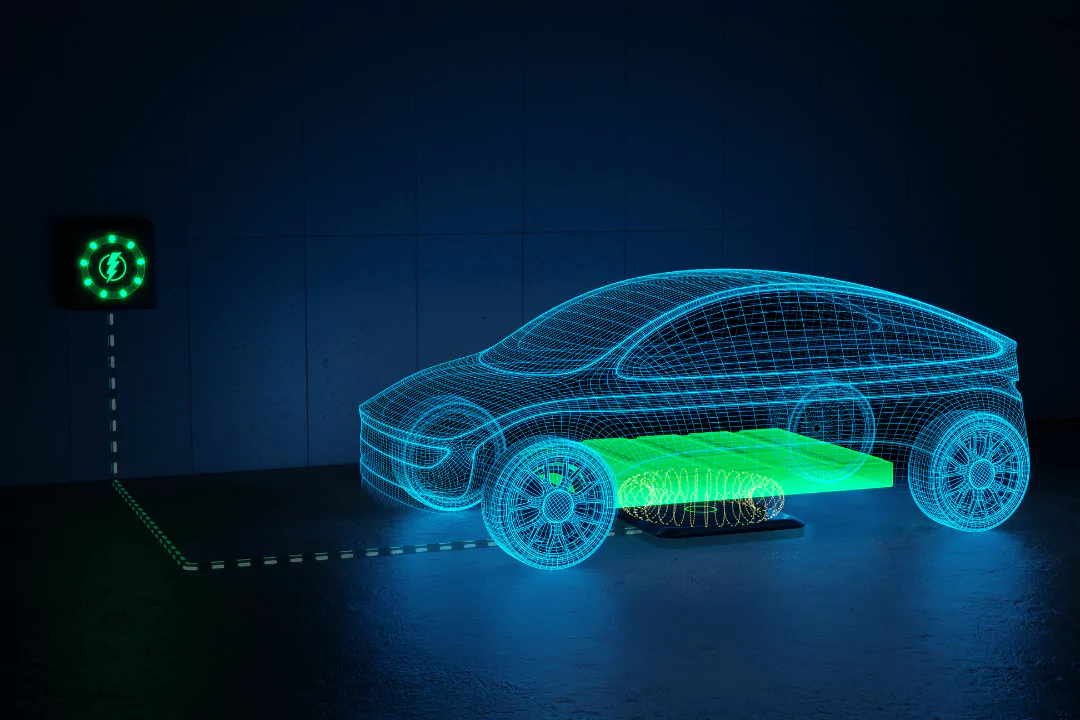
- Energy Management: AI turns into an energy coach, managing consumption like a pro. It can help extend your EV’s range and boost battery longevity, ensuring every drop of energy is used efficiently.
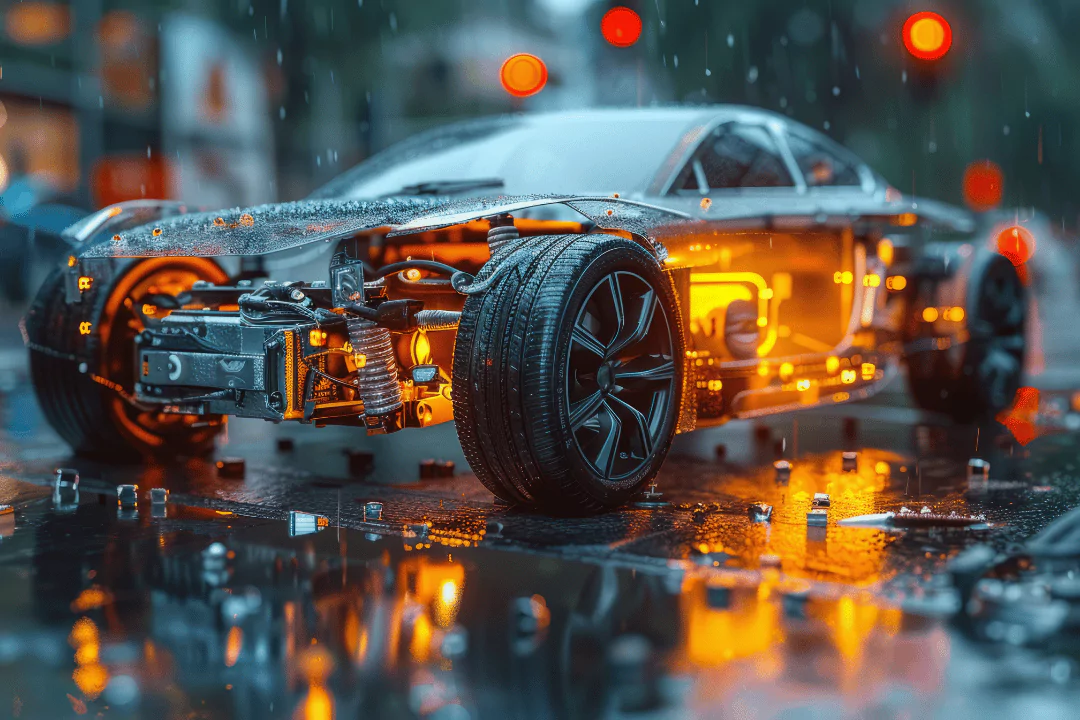
- Advanced Testing and Validation: By creating digital twins of their vehicles and simulating crash scenarios, OEMs can identify potential weaknesses and improve safety features before physical testing. This not only reduces development costs and time, but it also enhances the overall safety and performance of their EVs. By accelerating the CAE process powered by AI, digital prototypes are way quicker with simulating unusual and extreme operating conditions concerning stress, temperature, and electrochemistry variations to mention a few.

- Predictive Maintenance: By analysing data trends, AI can predict and prevent breakdowns before they happen. It can suggest preventive measures to reduce downtime and reduce maintenance costs. Loaded with historical data, these digital twins can help your EV run smoothly and enhance the overall driving experience.
Traction motor Digital Twins are simulated on various drive cycles, providing information such as winding temperature, casing temperature, bearing lubrication level, and the remaining useful life of permanent magnets. Similarly, traction battery Digital Twins provide information such as State of Charge (SoC), State of Health (SoH), cell temperatures, etc. These factors are considered for alternative material selection and cooling strategy alterations. These iterations are employed in the early design stage, reducing the time and cost of development.
The Digital Twin (DT) technology for Electric Vehicle (EV) motors and battery development involves a comprehensive framework that integrates various software and design elements.
This comprehensive framework brings together all the best tools and tricks to create the ultimate virtual EV experience.
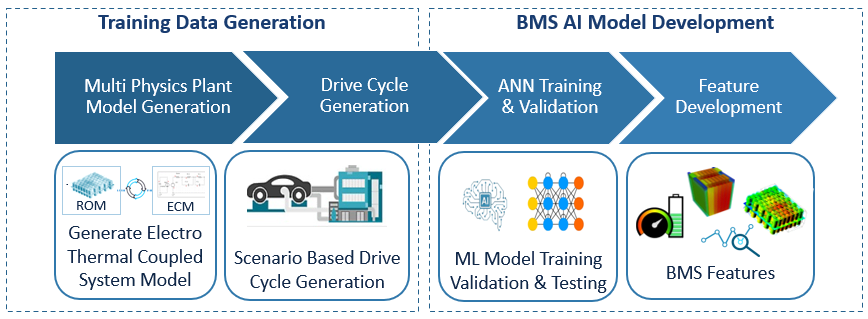
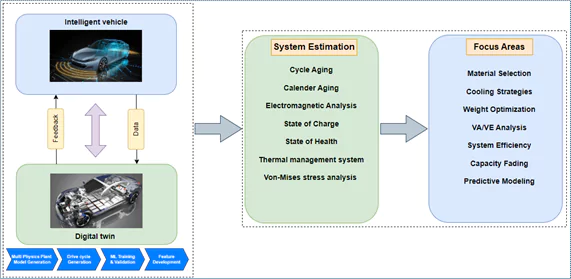
Tata Elxsi Use Cases
Leveraging AI for Intelligent Battery Monitoring
Objective – To continuously monitor the battery state and provide real-time insights about the operational characteristics and health of the battery.
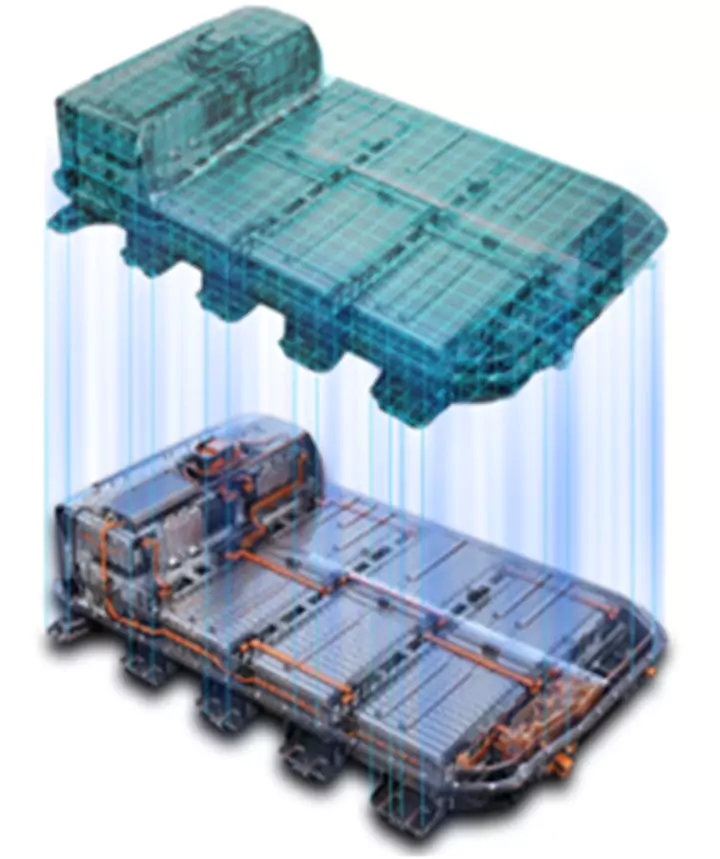
Key Highlights
- Accurate estimates of battery SoC
- Enabler for accurate range prediction
- Temperature estimation and anomaly prediction
- Virtual sensors to reduce hardware complexity and cost
- Enabler for enhanced Testing and Validation of BMS
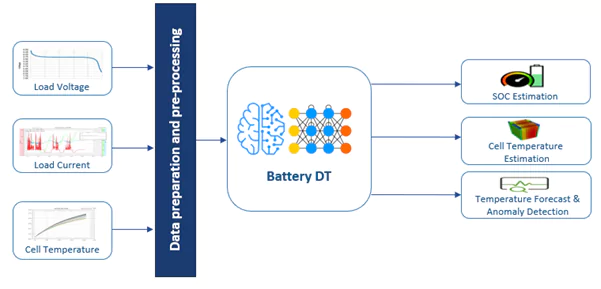
GenAI-based EV Twin for Range Prediction
Objective – To develop a digital twin for EV to provide accurate prediction of range.
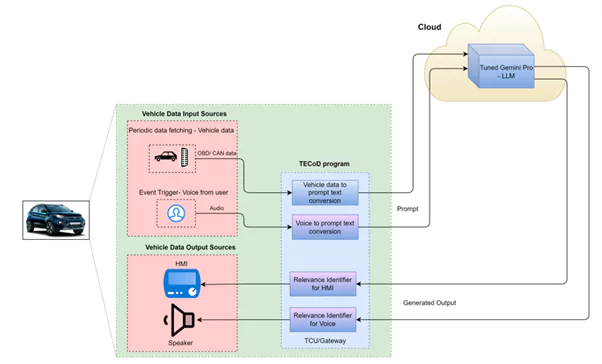
Here, a fine-tuned Gemini based LLM was used. The large language model takes real-time vehicle operational data along with map and weather information, to enhance driver efficiency and comfort.
Key Highlights:
- Range prediction using GenAI based DT
- Driver characterisation
- Real-time tracking of vehicle and traffic
- Drive analytics and insights
- Enhanced user experience
Gen AI-Based Co-Pilot for Digital Twins
The integration of Generative AI (GenAI) Co-Pilot for vehicle design with Digital Twin (DT) development for battery and traction motors marks a transformative leap in the automotive industry.
GenAI’s ability to generate numerous design iterations based on constraints complements Digital Twins evaluation of critical conditions, enhancing electromagnetic and thermal analyses. This synergistic approach optimises design through iterative virtual testing, reducing potential failures, time, and costs during physical validation. The feedback loop continues until an optimised design is achieved, accelerating product launches to market.

GenAI seamlessly integrates data across every stage of vehicle design and use, linking traction motor performance to battery wear and tear. This holistic optimisation boosts energy consumption and sustainability. GenAI also steps up in choosing the best topologies and materials, nailing down cooling strategies, and optimising power use in the coolant system. Plus, it fine-tunes active balancing for sustainable cell performance and tweaks motor efficiency based on battery aging, extending battery life and vehicle range.
This integration underscores a paradigm shift towards efficient, sustainable, and optimised vehicle design and operation.
How EV-olutionary! AI and Digital Twins will change the future EV’s
The future of AI-powered digital twins in electric vehicles (EVs) promises transformative advancements across the entire lifecycle of EV motors and batteries. As AI keeps evolving, its partnership with digital twins will spark key innovations and improvements.
AI-driven digital twins will get savvier at predicting maintenance needs and preventing unexpected breakdowns. With real-time data analytics, they will enable continuous monitoring and proactive management of EV components to ensure peak performance and longer lifespans for motors and batteries.
The design and development game will change forever with advanced simulation and virtual testing. AI-enhanced simulations will speed up iterations and optimisation of EV components, slashing the need for physical prototypes and dramatically cutting development time and costs. The digital twin’s ability to virtualise motor and battery models for mechanical structure, electrical components, and control systems and simulate numerous drive cycles and environmental conditions assist in material selection, cooling strategies, and weight optimisation of the respective system rapidly. Gen AI-based digital twin aids value analysis and value engineering activities with virtual simulation and identifying areas of interest for optimization.
AI will play a critical role in optimising energy consumption and improving the efficiency of EV systems. By managing energy use more effectively, AI-driven digital twins will help extend the range of EVs and enhance battery life, all while making it greener and more sustainable.
The future will see a seamless integration of AI-driven digital twins with autonomous driving technologies. This will enhance the safety, reliability, and efficiency of autonomous EVs, paving the way for more widespread adoption of self-driving vehicles.
The potential of AI-powered digital twins for EV motors and batteries is enormous. These advancements will not only supercharge the performance and reliability of EVs but will also drive a more sustainable and efficient automotive industry. By staying at the forefront of AI and digital twin technology, the automotive sector is set to lead the charge into the next era of electric mobility.
Authors
Perumal A.T.
Head of Electrification CoE, EV / FCV – Mechanical and Electromechanical Design, Tata Elxsi
Perumal A.T. is the Head of Electrification CoE at Tata Elxsi, with over 23 years of experience in mechanical and electromechanical design for electric and fuel cell vehicles. He specialises in high-voltage batteries, eMotors, eAxles, power electronics, and fuel cell stacks. Throughout his career, Perumal has contributed to significant advancements in hybrid and electric vehicle design, with extensive experience in both vehicle integration and engine systems. His expertise in electrification has been pivotal in driving innovation and excellence in the automotive industry.
Anush G Nair
Technology Manager - Software Controls and Electrification Practice, Tata Elxsi
Anush G. Nair is a Senior Technology Manager in the Electrification Practice group at Tata Elxsi. With over 22 years of industrial experience, including 16 years dedicated to automotive electronics and electric vehicle (EV) systems, he has developed a strong foundation in EV fundamentals, control systems, and model-based design. Anush has collaborated with major vehicle manufacturers and suppliers throughout his career. His current focus areas include Battery Management Systems, Traction Motors, Vehicle Architecture, and Digital Twin technology.